April 13, 2022
ChromaChecker 5 step Implementation for Production Inspectors
|
|
Define Production Standards applicable to every job, every printer, every operator |
|
|
Integrate new printing devices to ensure they match existing printers – compare to reference and compare to one another |
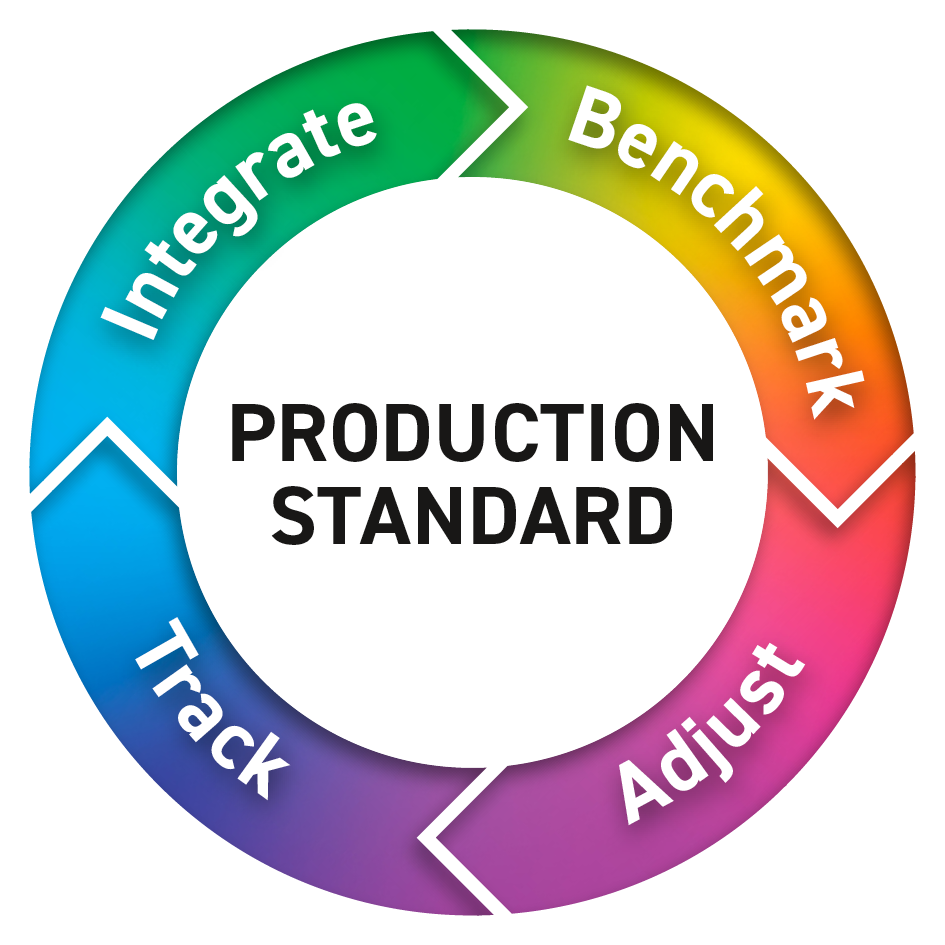 |
Benchmark printers, check for precision and accuracy |
Monitor printers on a job / daily basis (Show weekly reports per printer/operator) |
Adjust as necessary to bring into alignment (G7 Curves / ICC Profiles) – eliminate dedicated press runs |
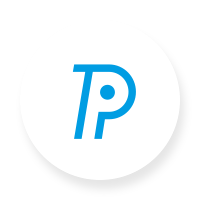 |
|
Get printer production under control:
- Define Job Standard applied to every job, every printer, every operator
- Benchmark printers, check for precision and accuracy, understand where the printer is
- Adjust as necessary to bring into alignment (G7 Curves / ICC Profiles) – eliminate dedicated press runs
- Track printers on a job / daily basis (Show weekly reports per printer / operator)
- Integrate new printing devices to ensure they match existing printers – compare to reference and compare to one another
|
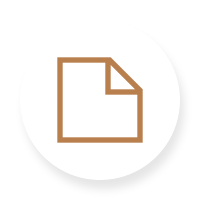 |
|
Get substrates under control:
- Define Job Standard
- Benchmark substrates in line with print
- Adjust as necessary to minimize the number of curves, profiles
- Track over time
- Integrate new substrates
|
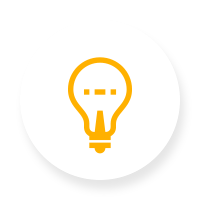 |
|
Get light booths under control:
- Define standard quality metric – E-Factor or ISO 3664
- Benchmark light booths
- Adjust as necessary
- Track over time to ensure bulbs are valid
- Integrate new light booths
|
|
|
Get displays under control:
- Define standards for tolerancing
- Benchmark displays
- Adjust as necessary
- Track over time
- Integrate new displays
|
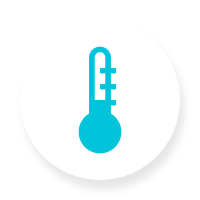 |
|
Get environment under control:
- Define standard based on the requirement
- Benchmark room environments
- Adjust as necessary
- Track over time
- Integrate new environments
|
Contact ChromaChecker Support
Additional information and Support Form is available for logged users.